Bob Magill Letterpress Feature

by Lizzy Tatlow
This article follows and dives deeper into the process of Bob Magill and how he works collaboratively with others as a printer and as a caster at Sterling Type Foundry in Union, MO. He discusses why he enjoys casting type, advice for younger printmakers and how he began his journey into the world of letterpress printmaking.
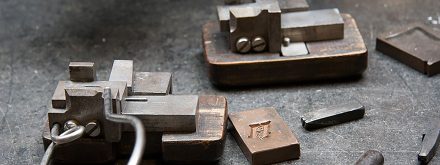
Bob Magill, of Sterling Type Foundry, has been a part of the letterpress community since the 1970’s- but he found his way to letterpress an unconventional way, as his main career path was not letterpress printing.
Magill worked as a Botanist at the Missouri Botanical Gardens and began by resetting type for various books that would be sent over in galleys.
Magill said, “They were hand-setting type for these books, they would go to a line and it would pop out and scatter the letters, but didn’t know what it said. That kinda got me interested in hand-set type. That kinda was kind of when, about that time, they started to do computer work. [I] Started getting interested in printing – into a group of letterpress printers.”
Handsetting Type
Typesetting is the process of arranging material of type into a form to be used in printing- in this case, type made of metal.
Before typesetting became a digital process, mistakes had to be fixed individually by hand, as well as each page being printed individually. This yielded a tedious process that required a lot of double and triple checking for mistake and error.
Magill said, “I got into typecasting because I was interested in making my own [type] so I wouldn’t have to worry about either used, old, battered type, or a font that I liked that was short of certain letters. That’s how I got into those [two] areas of letterpress.”
Helping to rearrange handset type helped Magill find his way into creating new metal type, to ensure that mistakes were minimal when others began to set their type into a form to print on press.
While he began by resetting galleys- metal trays in which a setting of type is placed, Magill began to develop his own passion for letterpress through an appreciation for the process through resetting type.
The Typecasting Process
What is typecasting you may ask? According to Merriam-Webster, casting is “to give a shape to (a substance) by pouring in liquid or plastic form into a mold and letting it harden without pressure”.
In letterpress printmaking, the person who casts the type gives shape to different typefaces through this process of pouring molten metal into brass settings called matrices.
Magill says, “it’s hot and a little dirty- although it’s not too bad, it’s not like the old days where they were using coal. There’s still a lot of oily grimy stuff. Again, I’m interested in how this all works, how do you make type, how do you align it, how do you get the precise measurements… I can pretty much make what I need and go and do that, partially what I was interested in.”
Creating type from scratch lets Magill create typefaces for printers that may need something special for a specific project, and to reduce barriers for others when creating a form for a potential lockup of a work.
By creating new type, Magill can be hands-on, as well as play an integral role in the preservation of the art of letterpress printmaking.
Magill says, “I print because i’m interested in typesetting and seeing how the letters, cuts and stuff go together and how you get that on the machine and print that and what it looks like, you know. So it’s more of an interest in how this all goes together. Like I have a linotype, I was just fascinated by all the gears and mechanisms that made this thing work but I don’t use it that much, but I have got it and cleaned it up and know how it works. That’s the kinda thing, I am just interested in how it all goes together.”
Moreover, for Magill, the process is just as important as the final product that printing creates. By creating new metal types, he can ensure that the printing process goes as smoothly as possible by making sure designers have the type they need to create each form seamlessly.
Magill says, “I like the handsetting of the type and making things work, how do you get small caps to fit or special characters that you need that aren’t the right size, so how do you make the 14 pt fit in the lockup.”
His work as a caster of type is an integral part of preserving the rich history of letterpress printmaking by casting types for different projects for printers.
Magill offers a necessary lens into the process of letterpress by viewing each piece- creating type, setting, type and printing, as parts that fit together and all play an integral role. Without any part of the process, the puzzle is incomplete and cannot succeed.
Collaboration with Other Printers
As letterpress is a multi-step process, Magill has had the opportunity to collaborate with various printers to create works that have lasting impact.
Magill said, “I don’t really do it as a business- sort of, but I’m not interested in a big business. I’m interested in working with people doing special projects. There was this a few years ago at the RIT they did a commemorative to Gaudi, and I was making type for projects that his type for projects that he would do and that was interesting to participate in that project. To get a commemorative on the 150th birthday or something. We made this group of broad sides that went to the Library of Congress so it was a pretty fancy deal and a lot of cool printers.”
One of the takeaways of collaborating often with other skilled printers is that each printer has a niche that they bring their individual experience to, and therefore can provide insight and knowledge that can only be learned from hands-on experience.
When you can learn from others as well as yourself, there is a rich opportunity for multiple types of learning that only creates better work. However, for Magill this comes from the process of learning from other letterpress printers in the field.
Magill says, “It’s really fun, especially for me, I wasn’t into printing as a career or anything, those guys are important to me to know how things are done. A lot of the stuff that I do I work through and eventually figure out a way to make it happen, but with those guys they can look at your stuff and say, you know what, you over inked the press or don’t do letter spacing or your centering is off. You know and they can give you that information that you need to make that work.. And that was the nice thing you know, Some of those people know about inks and some of them know about paper and i’m always fascinated with people that know a lot about the types and the faces and families, So it’s kind of interesting to talk to them and get their expertise because a lot of them are full time printers.”
Just as students collaborate with professors to take their experiences and insights to aid their creative process, printers feed off each others’ pieces of advice to continue an environment of learning and betterment.
Stepping back from work and asking the advice of others’ is a part of the creative process that allows for the evolution of work and lets artists better themselves and others. Through the experiences of others, we can learn from mistakes while attempting to avoid them as well.
Main Takeaways for Young Printmakers
As Magill learns from other skilled printmakers, we can learn from his experiences and apply them into our practice as makers.
Through years of collaborating with other artists and playing a key role in the process of his work and of other artists’ work, Magill’s insight into the letterpress process gives a deeper understanding to the creation of typefaces and how all parts of the process work together to create a beautiful whole piece.
Magill says, “I guess the biggest advice was actually in the film that Erin made, Dave Church, he was just saying that the equipment and the type are going away fairly quickly. It’s been a long time since it was the primary source of printing… you need to get what you need pretty quickly, and there are sources for the presses. If you have to have a windmill or something you’ve got to start that search early and be pretty [] about finding people. It’s getting more and more difficult to find. Decide what you want and go ahead and be pretty sure about where you want to end up. They’re still around now but they’re not gonna be around forever. Get some equipment and try to save it for the next generation and pass it on to others and try to interest others in the art of letterpress printing.”
Interviewed and Written by Lizzy Tatlow